What Kind of Flat Roof Do You Have?
What Kind Of Flat Roof Do You Have?
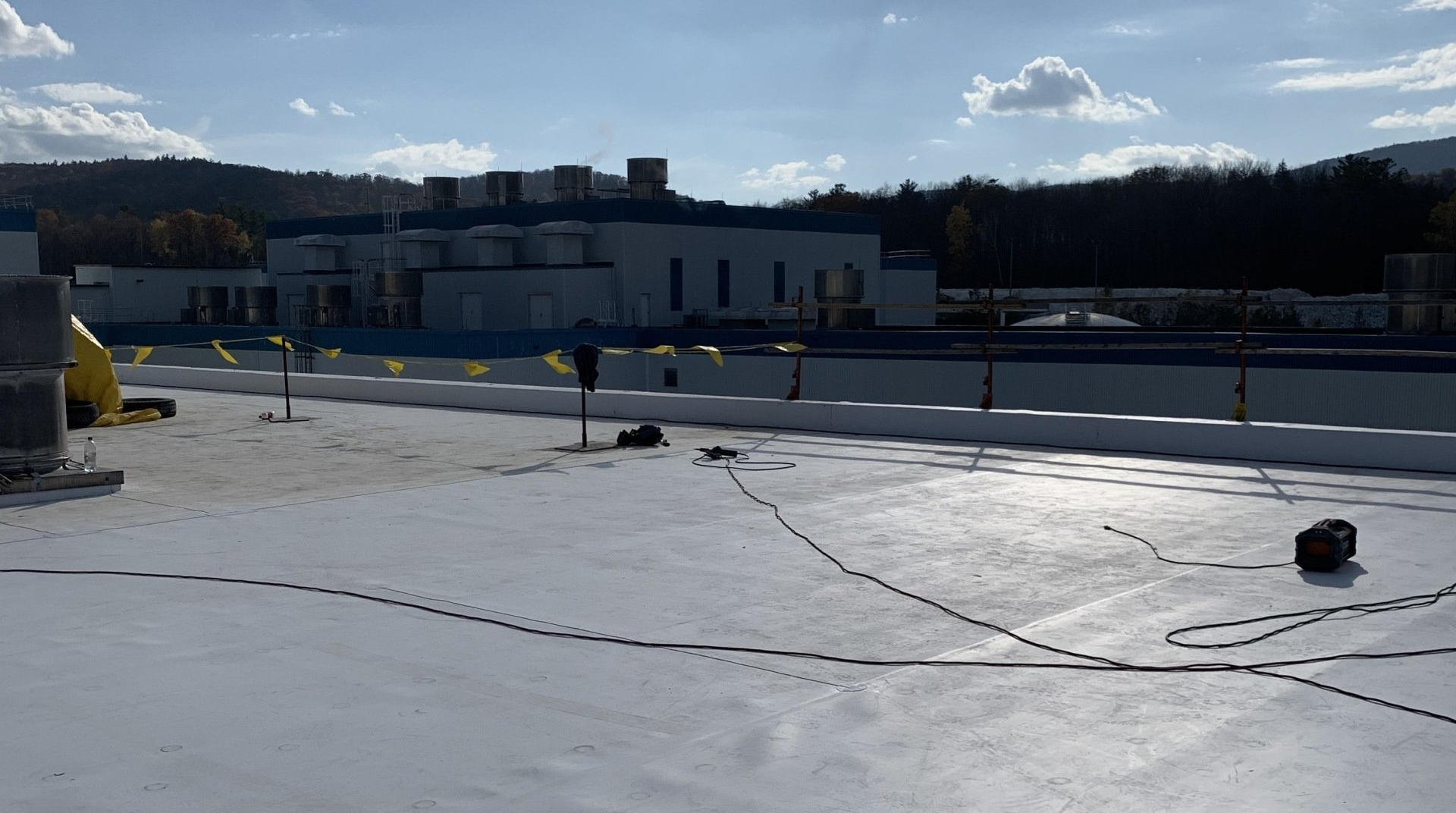
There is no such thing as a one-size-fits-all solution for flat roofs, which is why there are so many various types of flat roofs. Knowing what sort of flat roof your business or industrial building has affects what you may expect in terms of repairs and how long your roof will last. Depending on your building's needs, different flat roof styles have varied payoffs. If you've never built or repaired a roof before, here's a summary of the many types of flat roofs and how to tell them differently.
METAL ROOFS
If your flat roof is made of metal, you'll be able to tell right away. If the metal surface isn't painted, it should be visible, and it's probably patterned with indentions every few inches to a foot. Steel or aluminum are the most typical materials used. Metal roofs, which are technically low-sloped roofs, are still used today, although their popularity is waning as more commercial and industrial roofing solutions become available.
Metal roofs offer the advantage of having greater upfront expenses but a longer lifespan. Metal roofing, on the other hand, is a very permanent alternative, making it difficult to replace; in most cases, the old roof will need to be fully ripped off in order to install the new one, whereas other flat roofing designs allow you to build a new layer of roofing on top of the old one. All roofs, regardless of material, will be damaged at some point, and rusting is the most common problem with metal roofing. Your roof's strength will be weakened if it rusts, and it may develop holes until the damage is repaired.
POLYURETHANE SPRAY FOAM COATINGS
A top coat is applied to polyurethane spray foam roofs (also known as SPF) to ensure that your roof is completely watertight. You most likely have a polyurethane flat roof if your roof is reflecting white or gray in color and has a sprayed-on pattern. SPF is installed by spraying base layers of dense polyurethane foam over the roof's surface with a sprayer or wand. Following that, a waterproof silicone coating (usually gray or white) is applied to seal in the roof with an elastomeric foam layer.
Many commercial building owners are attracted to polyurethane roofing because of its flexibility and watertight barrier. Because of the flexibility of the materials, which can expand and contract as the outside temperature varies throughout the year, cracking and splits are less frequent. To make repairs, unlike metal flat roofs, you don't have to pull off the old roof materials; instead, a new layer of spray foam can be applied on top. The disadvantage of installing a polyurethane spray foam roof is that it can only be done in certain weather conditions. Because SPF cannot be installed if there is any ice, frost, or surface moisture on the existing roof, planning ahead of time might be problematic.
ASPHALT ROOFING
BUILT-UP ROOFING (OR BUR)
Does your roof have a tar or gravel appearance? Is there tar on the flashings around your HVAC curbs? Then you most likely have BUR, or built-up roofing. Built-up roofing has been established for more than a century, making it the flat roofing method with the most experience. A flexible, continuous membrane is generated in an asphalt BUR installation by alternating fabric layers (plies) with tar and aggregate layers. Instead of the asphalt shingles that are frequently seen on sloped roofs on residential structures, this forms a single membrane.
Asphalt BUR roofs are more waterproof than many other roofing styles, and they are also more fire resistant due to the gravel layers. Ultraviolet ray shielding is also provided by the aggregate. However, there are some disadvantages to this roofing design, just as there are to other roofing styles. Built-up asphalt roofs take longer to install than other roofing materials, and the process is often hazardous. This type of roofing is also more susceptible to wind and water damage than other types of roofing.
MODIFIED BITUMEN (OR MOD BIT)
Modified Bitumen Roofing (MBR) is a more current, up-to-date variant of asphalt BUR. Mod bit roofing is sometimes known as "rubber roofing" due of its elasticity, which gives it a rubber-like look. You most likely have a modified bitumen roof if the seams are roughly 3 feet apart and the texture is granular, comparable to that of an asphalt shingle up close. Most of the time, these roofs are constructed in a two-ply system with a cap sheet, or top layer, that produces a granular texture similar to asphalt shingles.
SINGLE-PLY MEMBRANES
EPDM/THERMOSET ROOFS
This is a typical rubber roof. The material used for membrane roofs is EPDM, which stands for Ethylene Propylene Diene Monomer. You most likely have an EPDM roof if your roof looks to be covered in rubber and the HVAC curbs or roof flashings are likewise covered in rubber. The roof will most likely be black in color if it has been attached. It is covered in large stones or other ballast that can be removed to expose the rubber roof surface if it is ballasted.
EPDM roofing materials are usually inexpensive, making them a popular choice for many business owners. If properly installed, they also provide fire protection and are a longer-lasting roofing option than many others. EPDM roofing has some drawbacks, including a higher installation cost when fully attached and a higher risk of punctures when not strengthened. In addition, black rubber roofs are less visually appealing than other roofing alternatives.
TPO AND PVC/THERMOPLASTIC
Another single-ply membrane roofing option is TPO (thermoplastic polyolefin) or PVC (polyvinyl chloride). Your roof is most likely TPO or PVC if it is light or white in color and is drawn taut over the building, like a white rubber roof. The single-membrane roofs are adhered to the structure or mechanically attached using screws.
TPO roofs are built to last, with one of the longest lifespans of any flat roofing material. They are wind, fire, and chemical resistant, as well as watertight. The disadvantage of TPO roofs is that they require the removal of your existing roof in order to be installed, but this offers a stable foundation for the waterproof seal. Because of its resilience to chemicals that it may be subjected to in an industrial setting, TPO is a popular material for many industries. TPO roof installation is one of Rodd Roofing's specialties, and we feel it is one of the most durable materials available, with the best return on investment due to its extended lifespan.