How Can Single Ply Roofing Benefit You?
The Benefits of Single-Ply Roofing
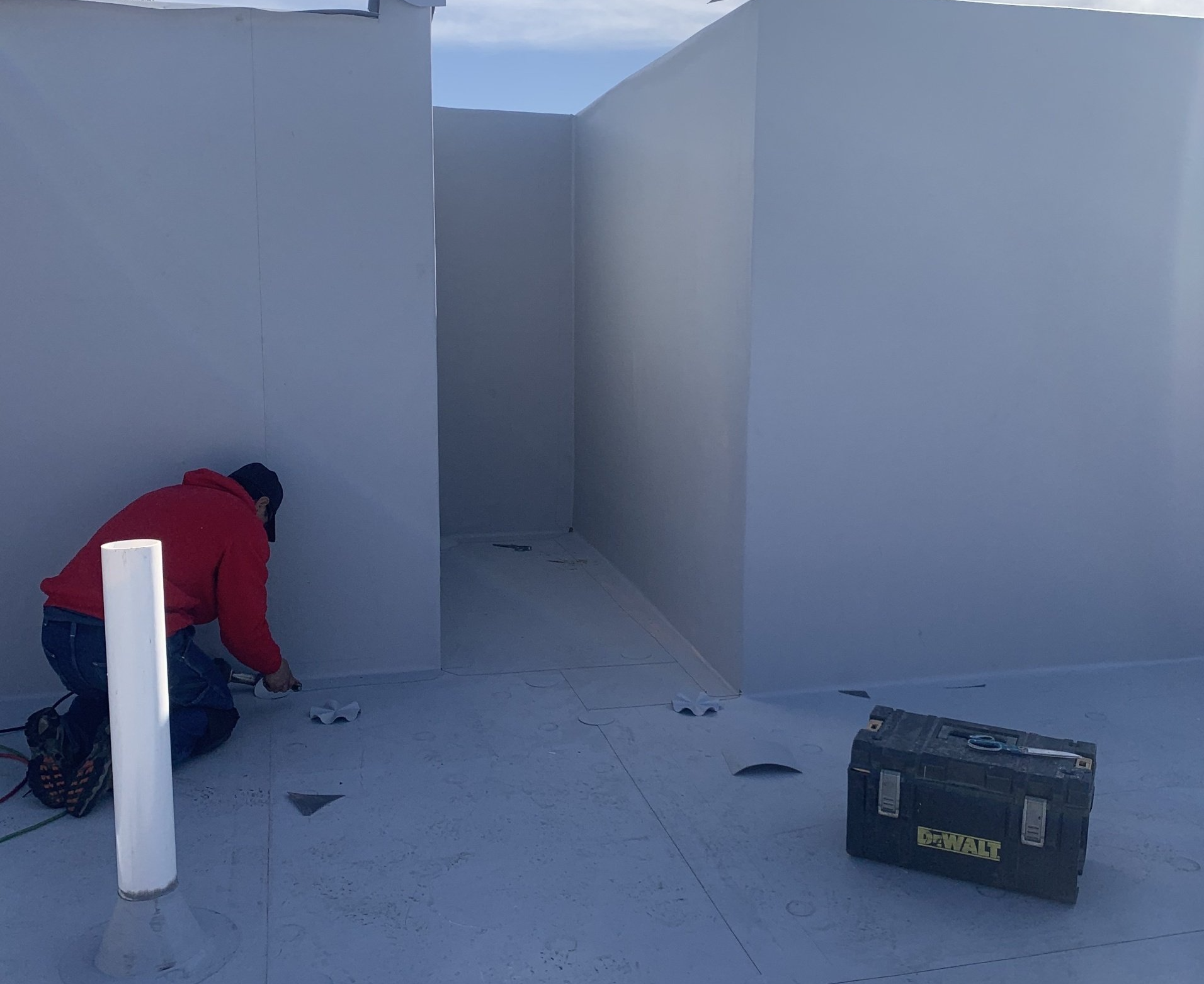
The oil crisis in the 1970s demonstrated the need for roofing alternatives to petroleum. A variety of lightweight flexible roofing membranes were on the market to meet this need. They were simple to install and came with a long list of acronyms, including PVC, EPDM, CPE, CPA, PIB, CSPE, NBP, EIP, and others.
Let's jump to the twenty-first century now. The alphabet soup of single-ply acronyms has been whittled down to the most often heard: PVC, EPDM, and TPO after decades of altered formulations, changing environmental restrictions, and strong rivalry. New installation methods have been created to add to the mix. All of these developments necessitate that single-ply roofing be chosen with caution and preparation.
Single Ply Roofing is not only lightweight and a high performing roof but is resistant to all weather conditions, temperatures, and those made from EPDM, TPO, and PVC typically last between 15-25 years.
For property owners and managers of commercial and industrial properties, there are a huge range of benefits in choosing single ply membranes for any flat roof. An increasing number of homeowners are also using this roofing material for home extensions, outbuildings and garages etc. This really showcases the adaptability of single ply roofing as the material can be implemented on any type of building with a flat roof. Before deciding which single-ply technology to utilize, a facility executive must first determine whether the structure is suitable for a single-ply membrane. When it comes to roofing, "one size fits all" is just as false as it is when it comes to apparel. A single-ply membrane is appropriate in the following situations:
- When weight is a consideration.
- When some movement may be expected in the building structure.
- When re-covering an existing membrane.
- When the building is wide open and large panels can be used.
- When reroofing structural standing seam metal roof assemblies.
- When roofing in cold weather (with some precautions).
- When installing a green roof.
- When a light-colored system is desired.
Some of the key benefits include:
- Simple & easy to install
- This results in lower installation costs as the stress-free installation reduces the time needed to fit the roofing.
- Exceptional weather resistance
- With the unpredictability of European weather, Single Ply Roofing remains resistant in all types of weather. The rubber is waterproof & freeze proof as well as being resistant to UV rays. This means less deterioration and consequently less repairs.
- Durable with resistance to tears and punctures
- Cost-effective roofing material
- As the material is not easily torn or punctured, this means there is less potential for storm damage.
- Fleece-backed membrane for bonded applications and unbacked for mechanically fixing
- Provides a flat & level surface for equipment such as HVAC units
- No chlorides, fluorides or plasticisers present in the single ply membranes.
- No carcinogenic fumes present during installation
- Available in both light & dark grey
There are also many additional benefits to consider when considering Single Ply Roofing:
- A removed single-ply flat roof membrane can be recycled
- Can be easily converted/adapted for green roof installations
- Resists damage from UV rays – fewer repairs/less deterioration
- Suitable for overlaying existing roofs
- Can be repaired and rewelded years after installation
- Airtight construction
- Lightweight ability
- Root proof without further protection (FLL Factor)
- Absorbs thermal movement
- Square-grid pattern finish which aids slip resistance
- Offer ease-of-access for purposes of maintenance, repairs
Thermoplastic Membranes: PVC and TPO
Thermoplastics and synthetic rubber are the two most common types of single-ply membranes. (Because modified bitumen membranes are almost never erected as single-ply membranes, they are not covered in this article.) Thermoplastics have a unique property that synthetic rubbers lack: they can be heated and molded or melted repeatedly. As a result, heat-welding is the most frequent method of seaming a thermoplastic membrane. The membrane is fused into a strong bonded seam when the edges are properly melted together.
Currently, there are two primary thermoplastic membranes on the market. Polyvinyl chloride (PVC) and thermoplastic polyolefin (TPO) are two among them (TPO). KEE, the third, is made by a single company. The membrane is famous for being able to withstand being hit by a two-by-four shot from an air cannon, despite its limited application.
With the first PVC-based systems deployed in Europe in the early 1960s, PVC roof membranes have the longest track record of any thermoplastic membrane. Vinyl membranes are self-extinguishing by nature, allowing them to receive fire ratings from Underwriters Laboratories and Factory Mutual, as well as perform consistently in real-world flame exposure.
Polyester or fiberglass reinforcing, vinyl resins, ultraviolet light inhibitors, heat-stabilizers, biocides, pigments, and plasticizers are all found in the completed vinyl roof membrane. Polyester reinforcement gives mechanically fastened roofing systems the tearing and breaking strengths they require. Plasticizers are used in the formulation because PVC is not naturally flexible. The loss of plasticizers in un-reinforced membranes has previously resulted in catastrophic failures as the membrane reverted to its inflexible form and fractured in cold temperatures. All PVC membranes are now strengthened, and new formulas reduce the membrane's loss of plasticizers.
In the last ten years, TPO membranes have become increasingly popular as roof membranes. Polypropylene and ethylene-propylene (EP) rubber are polymerized together utilizing state-of-the-art polymer manufacturing technology to create a TPO roofing membrane. Without the use of polymeric or liquid plasticizers, this approach allows for the creation of TPO membranes that are flexible at low temperatures.
The TPO polymer does not include chlorine, and no chlorine-containing chemicals are added during sheet production, unlike some other common thermoplastic roofing membranes.
To develop a product that can endure the conditions associated with rooftop exposure, the TPO resin is combined with other components such as a weathering package, fire retardants, and colors. TPO is not fire resistant by itself, so it must be treated with fire retardants to achieve a fire rating. The proportions of weathering material and fire retardants vary from one manufacturer to the next. TPO membranes, unlike PVC membranes, are inherently flexible, therefore no additional plasticizers are required in the formulation, reducing the risk of plasticizer migration.
Synthetic Rubber: EPDM
EPDM is the most used synthetic rubber roof membrane. Synthetic rubber is a thermoset, which means it cannot be melted and reformed once it has hardened. As a result, an adhesive — usually a field-applied contact cement or an adhesive tape that is placed in the field or factory and activated by removing a release paper — is used to seal the rubber membrane. Because tapes are often easier to apply and less likely to be installed poorly, they have become the de facto norm.
EPDM membrane rolls can be up to 10 feet wide. Larger rolls necessitate fewer seams. Seam failure is less likely when there are fewer seams. EPDM is frequently used on structures with very big roofs due to the roll sizes. EPDM has the ability to stretch and relax, allowing it to easily tolerate thermal expansion and contraction on broad roof areas.
EPDM roof membranes, like PVC, have been manufactured for more than 30 years. Over time, the systems have been improved — reinforcement has been added, new seaming and flashing processes and materials have been developed, and white membranes and clean sheets have been introduced to reduce on-site dust contamination — but the core product remains the same and operates effectively.
The majority of thermoplastics are white, however pastel colors are also available. These white membranes have a high initial reflectance value, which can assist keep the roof and, as a result, the interior of the structure cooler. However, unless the roof is washed on a regular basis as it becomes older and acquires dirt, its initial worth will dwindle. The white surface of synthetic rubber is accessible, but the more durable membrane is dark grey in hue. There are white acrylic coatings for EPDM membranes that can provide the same reflectivity as thermoplastics and are claimed to extend the roof's life by up to 10 years.
A poor choice can result in an expensive disaster for any sort of roofing system. With so many options, choose which single-ply to use might be challenging. The choice is made considerably more difficult by building laws, regulations, and insurance needs. Single-ply membranes, on the other hand, can provide a long-lasting roof system at a reasonable cost if roofing needs are adequately assessed and supplies are appropriately chosen.
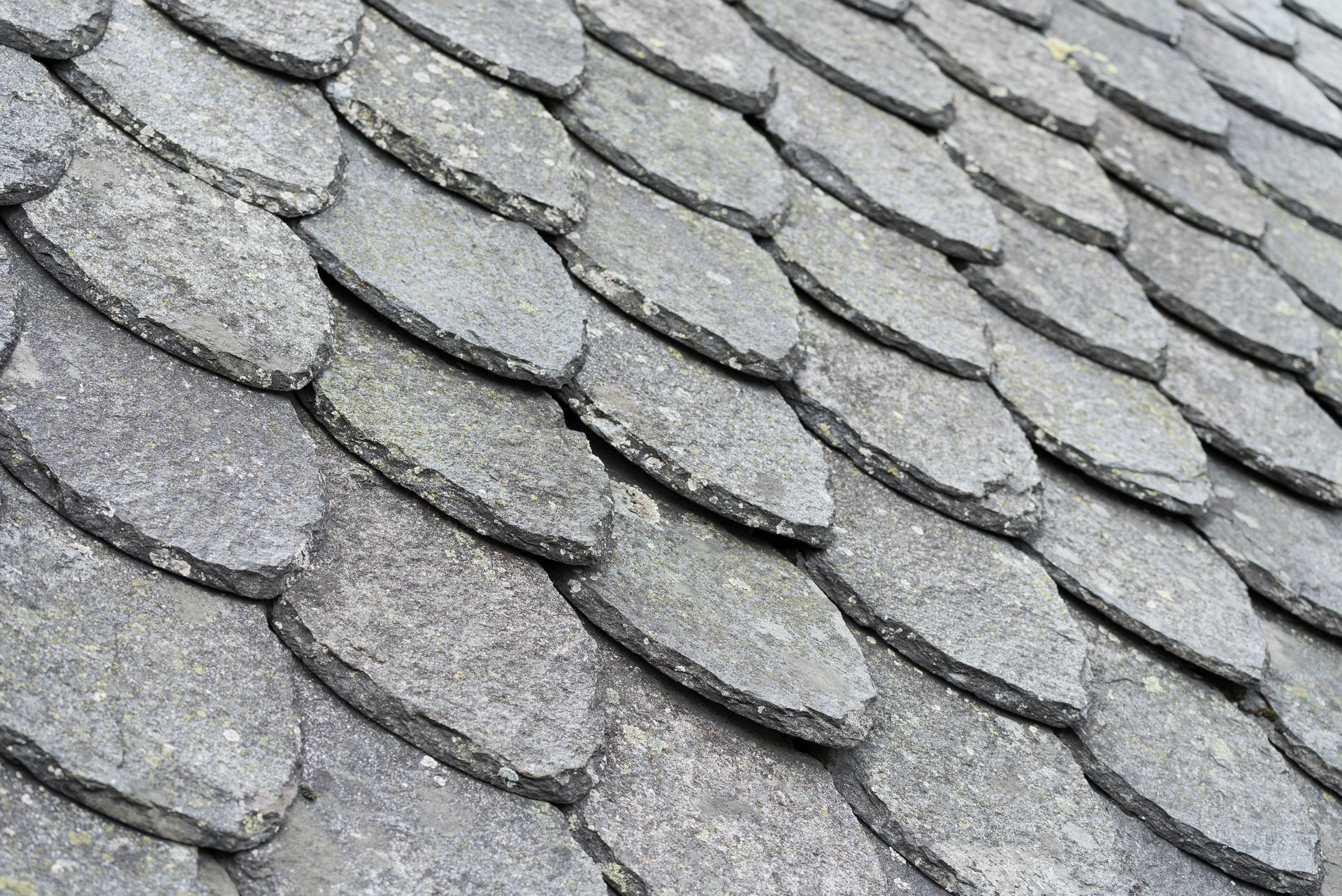